Have you ever wondered what belt slap is and how it impacts various industries? Belt slap refers to the phenomenon where a conveyor belt vibrates or flutters as it moves over rollers or pulleys. This seemingly minor issue can lead to significant problems in industrial settings, affecting productivity, safety, and equipment longevity. Understanding belt slap is crucial for engineers, maintenance professionals, and anyone working with conveyor systems.
In this comprehensive guide, we will explore the concept of belt slap, its causes, effects, and solutions. We'll also delve into real-world applications and provide actionable tips to mitigate belt slap in your operations. Whether you're a seasoned professional or new to the field, this article will equip you with the knowledge to tackle belt slap effectively.
By the end of this guide, you'll understand why addressing belt slap is vital for maintaining efficient and safe operations. Let's dive in and uncover the secrets behind this common yet often overlooked issue in conveyor systems.
Read also:Popeyes Corn On The Cob A Flavorful Delight For Every Corn Lover
Here's a quick overview of what we'll cover:
- What is Belt Slap?
- Causes of Belt Slap
- Effects of Belt Slap
- Solutions to Belt Slap
- Real-World Applications
- Best Practices for Preventing Belt Slap
- Tools and Technologies for Monitoring Belt Slap
- Case Studies
- Frequently Asked Questions
- Conclusion
What is Belt Slap?
Belt slap occurs when a conveyor belt experiences excessive vibration or fluttering as it moves over rollers, idlers, or pulleys. This phenomenon is often caused by improper tension, misalignment, or worn-out components in the conveyor system. While belt slap may seem like a minor issue, it can lead to significant operational challenges if left unaddressed.
Understanding belt slap is essential for industries that rely heavily on conveyor systems, such as manufacturing, mining, and logistics. By identifying the root causes of belt slap, professionals can implement effective solutions to enhance system performance and reduce downtime.
Key Characteristics of Belt Slap
Belt slap is characterized by:
- Unusual noise during operation
- Vibrations in the conveyor belt
- Increased wear and tear on components
- Potential safety hazards
Causes of Belt Slap
Several factors contribute to belt slap in conveyor systems. Identifying these causes is the first step toward resolving the issue. Below are some of the most common causes:
Improper Belt Tension
One of the primary causes of belt slap is incorrect tension settings. If the belt is too loose, it may flutter or vibrate excessively. Conversely, over-tensioning can lead to other problems, such as premature wear on components.
Read also:Exception Fashion Nova Your Ultimate Guide To Elevating Your Style
Misalignment
Misaligned rollers, pulleys, or idlers can cause the belt to move unevenly, leading to belt slap. Regular inspections and adjustments are necessary to ensure proper alignment.
Worn-Out Components
Over time, components such as rollers, bearings, and pulleys can wear out, causing irregularities in the belt's movement. Replacing worn-out parts is crucial for maintaining smooth operations.
Effects of Belt Slap
Belt slap can have several negative effects on conveyor systems and operations. These effects include:
Reduced Productivity
Excessive belt slap can slow down conveyor systems, leading to reduced productivity and increased downtime. This can have a significant impact on operational efficiency and profitability.
Increased Maintenance Costs
The wear and tear caused by belt slap can result in higher maintenance costs. Regular inspections and repairs are necessary to address the issue, which can strain budgets.
Potential Safety Hazards
Belt slap can pose safety risks to workers, especially in environments with heavy machinery. Addressing the issue promptly is essential for ensuring a safe working environment.
Solutions to Belt Slap
There are several solutions to mitigate belt slap in conveyor systems. Below are some effective strategies:
Proper Belt Tensioning
Maintaining the correct belt tension is crucial for preventing belt slap. Regularly check and adjust the tension settings to ensure optimal performance.
Regular Maintenance
Implementing a routine maintenance schedule can help identify and address potential issues before they escalate. This includes inspecting components for wear and tear and making necessary replacements.
Alignment Checks
Conducting regular alignment checks ensures that all components are properly aligned, reducing the likelihood of belt slap.
Real-World Applications
Belt slap affects various industries, including manufacturing, mining, and logistics. Below are some real-world applications where addressing belt slap is critical:
Manufacturing
In manufacturing plants, conveyor systems are essential for moving materials and products. Preventing belt slap ensures smooth operations and minimizes downtime.
Mining
Mining operations rely heavily on conveyor systems to transport materials. Addressing belt slap in these environments is crucial for maintaining efficiency and safety.
Logistics
Logistics companies use conveyor systems to sort and transport packages. Reducing belt slap improves the accuracy and speed of operations, enhancing overall performance.
Best Practices for Preventing Belt Slap
Adopting best practices can help prevent belt slap and maintain efficient conveyor system operations. Here are some recommendations:
- Conduct regular inspections and maintenance checks
- Ensure proper alignment of all components
- Monitor belt tension and adjust as needed
- Replace worn-out parts promptly
- Train staff on recognizing signs of belt slap
Tools and Technologies for Monitoring Belt Slap
Advancements in technology have introduced tools and systems to monitor and address belt slap effectively. Below are some examples:
Vibration Sensors
Vibration sensors can detect unusual vibrations in conveyor systems, alerting operators to potential issues before they become severe.
Condition Monitoring Systems
Condition monitoring systems provide real-time data on the performance of conveyor systems, enabling proactive maintenance and reducing downtime.
Automation and AI
Automation and artificial intelligence can analyze data from sensors and systems to predict and prevent belt slap, enhancing overall system performance.
Case Studies
Real-world examples demonstrate the impact of addressing belt slap in various industries. Below are two case studies:
Case Study 1: Manufacturing Plant
A manufacturing plant experienced significant downtime due to belt slap in its conveyor system. After implementing a comprehensive maintenance program and upgrading components, the plant reduced downtime by 30% and improved overall productivity.
Case Study 2: Mining Operation
A mining operation faced safety concerns due to belt slap in its conveyor system. By installing vibration sensors and conducting regular inspections, the operation eliminated safety hazards and improved system reliability.
Frequently Asked Questions
What causes belt slap?
Belt slap is typically caused by improper tension, misalignment, or worn-out components in conveyor systems.
How can I prevent belt slap?
To prevent belt slap, ensure proper tension, conduct regular maintenance, and check alignment regularly. Replacing worn-out parts promptly is also essential.
What are the effects of belt slap?
Belt slap can reduce productivity, increase maintenance costs, and pose safety hazards in industrial settings.
Conclusion
Belt slap is a common issue in conveyor systems that, if left unaddressed, can lead to significant operational challenges. By understanding its causes, effects, and solutions, professionals can implement effective strategies to mitigate belt slap and enhance system performance.
We encourage readers to share their experiences with belt slap in the comments section below. Your insights can help others facing similar challenges. Additionally, feel free to explore other articles on our site for more information on conveyor systems and industrial maintenance.
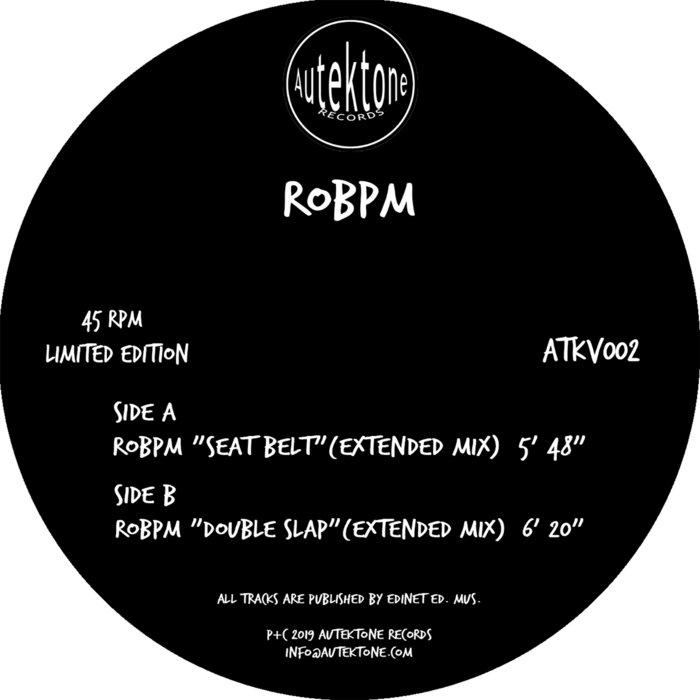
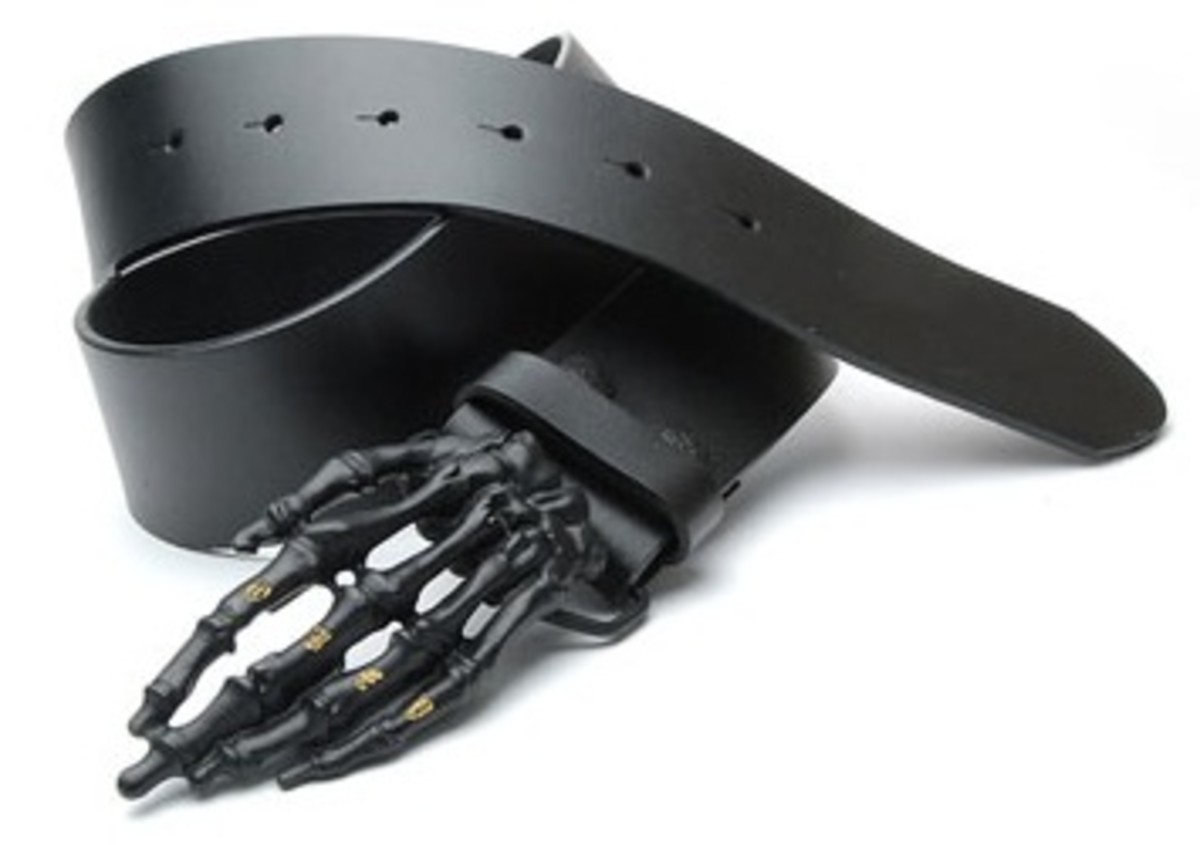