Defects per Million Opportunities (DPMO) is a critical metric used in quality management to evaluate process performance and efficiency. It plays a significant role in Six Sigma methodologies, allowing businesses to measure and improve their processes systematically. Understanding DPMO is essential for organizations aiming to achieve high-quality standards and reduce operational costs.
In today's competitive business environment, quality assurance has become more important than ever. Companies are constantly looking for ways to minimize defects and optimize their processes. DPMO serves as a valuable tool in this regard, providing a clear and quantifiable way to assess the effectiveness of quality control efforts.
This article will delve into the concept of DPMO, its significance, and how it can be calculated and applied in various industries. Whether you're a quality assurance professional, a business owner, or simply interested in learning more about process improvement, this guide will provide you with all the information you need to understand DPMO in text.
Read also:Thanksgiving Emoji Text Chain A Fun And Festive Way To Celebrate The Season
Table of Contents
- Introduction to DPMO
- What is DPMO in Text?
- How to Calculate DPMO
- Why is DPMO Important?
- Applications of DPMO
- Examples of DPMO in Practice
- DPMO vs. Other Quality Metrics
- Tools and Software for DPMO Analysis
- Challenges in Implementing DPMO
- The Future of DPMO in Quality Management
Introduction to DPMO
Quality management is an essential aspect of modern business operations. One of the key metrics used in this field is DPMO, which stands for Defects per Million Opportunities. This metric helps organizations identify areas of improvement and measure the effectiveness of their quality control efforts.
Origins of DPMO
The concept of DPMO originated from the Six Sigma methodology, which was developed by Motorola in the 1980s. Six Sigma focuses on reducing process variation and eliminating defects to achieve near-perfect performance. DPMO became a fundamental part of this methodology due to its ability to quantify the number of defects in a process.
Relevance in Today's Business World
In today's fast-paced business environment, companies are under constant pressure to deliver high-quality products and services. DPMO provides a standardized way to measure quality, enabling organizations to benchmark their performance against industry standards and competitors.
What is DPMO in Text?
DPMO is a statistical measure used to quantify the number of defects in a process relative to the total number of opportunities for defects. It is expressed as the number of defects per one million opportunities. This metric is particularly useful in identifying areas of a process that require improvement and tracking progress over time.
Read also:Does Nulastin Have Prostaglandins A Comprehensive Guide
Components of DPMO
- Defects: Any flaw or error in a product or service that makes it non-conforming to specifications.
- Opportunities: The total number of chances for a defect to occur in a given process.
- Million Opportunities: A standardized scale used to express the defect rate per one million opportunities.
Why Use DPMO?
DPMO is preferred by many organizations because it provides a clear and consistent way to measure quality. Unlike other metrics, it takes into account the complexity of a process by considering the number of opportunities for defects. This makes it a more accurate and reliable measure of process performance.
How to Calculate DPMO
The calculation of DPMO involves a straightforward formula that considers the number of defects, units, and opportunities. The formula is as follows:
DPMO = (Number of Defects × 1,000,000) / (Number of Units × Number of Opportunities per Unit)
Step-by-Step Guide to Calculating DPMO
- Identify the total number of defects in the process.
- Determine the total number of units produced or processed.
- Calculate the number of opportunities for defects per unit.
- Plug these values into the DPMO formula to get the result.
Example Calculation
Suppose a manufacturing company produces 10,000 units, and each unit has 5 opportunities for defects. If there are a total of 200 defects, the DPMO can be calculated as follows:
DPMO = (200 × 1,000,000) / (10,000 × 5) = 4,000
Why is DPMO Important?
DPMO is a crucial metric for organizations looking to improve their quality management processes. It provides a quantifiable measure of process performance, enabling businesses to identify areas of improvement and track progress over time.
Key Benefits of Using DPMO
- Standardization: DPMO offers a standardized way to measure quality across different processes and industries.
- Identifying Improvement Areas: By highlighting areas with high defect rates, DPMO helps organizations focus their improvement efforts where they are most needed.
- Benchmarking: DPMO allows companies to compare their performance against industry standards and competitors.
Impact on Business Performance
Implementing DPMO as part of a quality management strategy can lead to significant improvements in business performance. By reducing defects, organizations can lower costs, improve customer satisfaction, and increase profitability.
Applications of DPMO
DPMO is widely used across various industries to measure and improve process performance. Its applications range from manufacturing and healthcare to finance and software development.
Manufacturing
In manufacturing, DPMO is used to monitor production processes and ensure that products meet quality standards. By identifying and addressing areas with high defect rates, manufacturers can improve efficiency and reduce waste.
Healthcare
In the healthcare industry, DPMO is used to measure the quality of patient care and identify areas for improvement. For example, it can be used to track the number of medical errors or adverse events per million opportunities.
Examples of DPMO in Practice
Several organizations have successfully implemented DPMO as part of their quality management strategies. Below are a few examples:
Case Study: Motorola
Motorola, the pioneer of Six Sigma, used DPMO to improve the quality of its manufacturing processes. By reducing defects, the company was able to lower costs and increase customer satisfaction.
Case Study: GE
General Electric implemented DPMO as part of its Six Sigma initiative, resulting in significant improvements in process efficiency and profitability. The company reported cost savings of over $1 billion within the first five years of implementation.
DPMO vs. Other Quality Metrics
While DPMO is a powerful metric, it is not the only tool available for measuring quality. Other commonly used metrics include:
- Defects per Unit (DPU): Measures the average number of defects per unit.
- First-Time Yield (FTY): Measures the percentage of units that pass through a process without defects on the first attempt.
- Process Capability Index (Cpk): Measures the ability of a process to produce output within specification limits.
Advantages of DPMO
DPMO offers several advantages over other quality metrics, including its ability to account for process complexity and provide a standardized measure of quality.
Tools and Software for DPMO Analysis
Several tools and software solutions are available to help organizations calculate and analyze DPMO. These include:
- Minitab: A statistical software package widely used for quality improvement projects.
- SAS: A powerful analytics platform that supports Six Sigma methodologies.
- Excel: A versatile spreadsheet tool that can be used to calculate DPMO manually.
Selecting the Right Tool
When choosing a tool for DPMO analysis, it is important to consider factors such as ease of use, cost, and compatibility with existing systems. Organizations should select a tool that meets their specific needs and aligns with their quality management objectives.
Challenges in Implementing DPMO
While DPMO is a valuable metric, implementing it effectively can pose several challenges. These include:
- Data Collection: Gathering accurate and complete data can be time-consuming and resource-intensive.
- Complexity: Calculating DPMO for complex processes with numerous opportunities for defects can be challenging.
- Resistance to Change: Organizations may face resistance from employees who are accustomed to traditional quality metrics.
Overcoming Implementation Challenges
To overcome these challenges, organizations should invest in training and education, leverage technology to streamline data collection, and communicate the benefits of DPMO to all stakeholders.
The Future of DPMO in Quality Management
As businesses continue to prioritize quality and efficiency, the role of DPMO in quality management is likely to grow. Advances in technology, such as artificial intelligence and machine learning, will further enhance the ability of organizations to calculate and analyze DPMO effectively.
Emerging Trends in Quality Management
Some of the emerging trends in quality management include the use of predictive analytics, real-time monitoring, and automation. These technologies will enable organizations to identify and address defects more quickly and efficiently, leading to improved performance and customer satisfaction.
Conclusion
DPMO is a powerful metric that provides organizations with a clear and standardized way to measure process performance and improve quality. By understanding the concept of DPMO and implementing it effectively, businesses can achieve significant improvements in efficiency, cost savings, and customer satisfaction.
We encourage readers to take action by applying the principles of DPMO in their own organizations. Whether you're a quality assurance professional, a business owner, or simply interested in process improvement, DPMO offers valuable insights that can help you achieve your goals. Share your thoughts and experiences in the comments below, and explore other articles on our site to learn more about quality management and related topics.
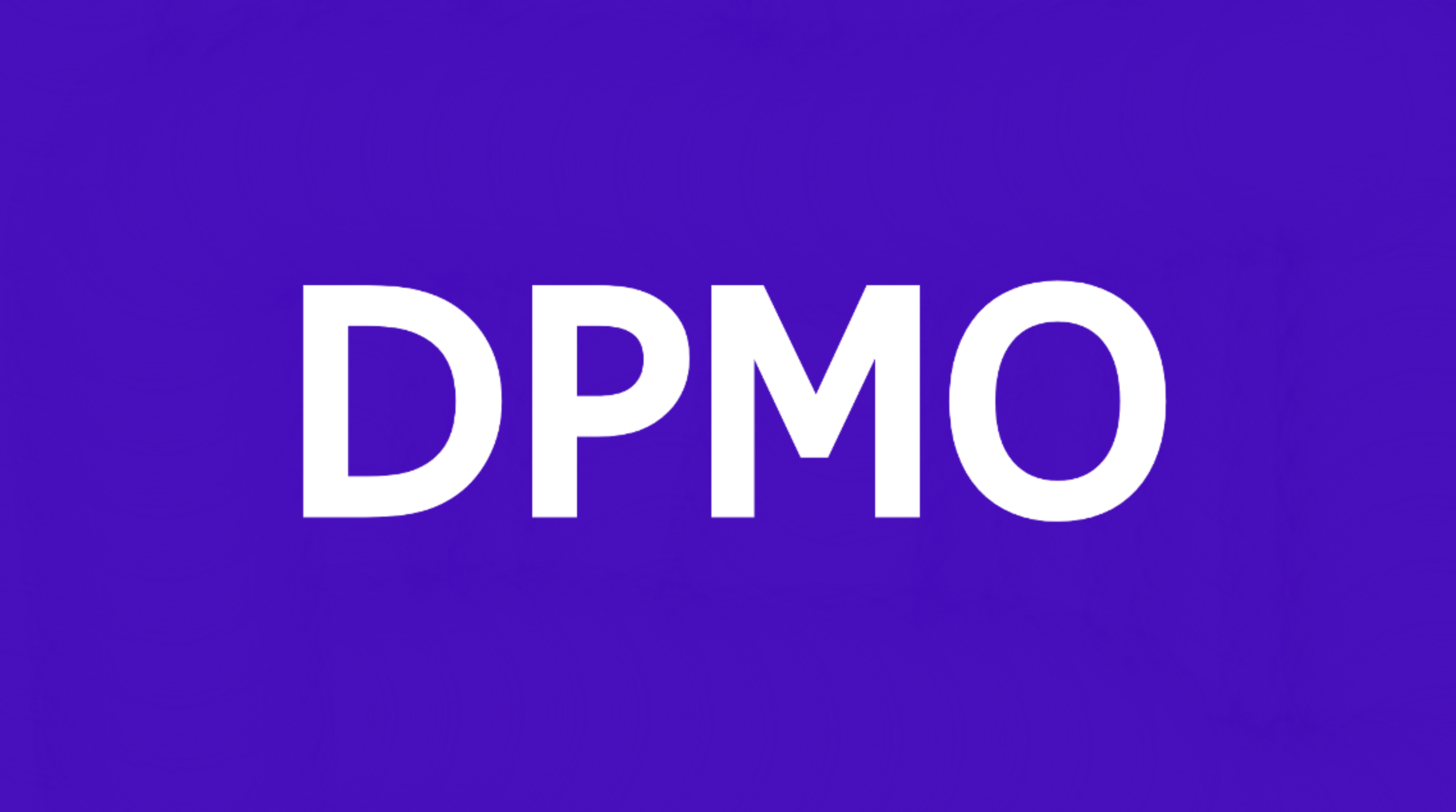